In the dynamic world of industrial operations, the automatic conveyor system has emerged as a cornerstone of modern manufacturing and distribution. Facilitating the swift and safe transport of goods across facilities, these systems enhance operational efficiency and optimize workflow. This article delves into the intricacies of automatic conveyor systems, highlighting their benefits, styles, and materials, and how they integrate into various industrial environments.
The Vital Role of Automatic Conveyor Systems
Automatic conveyor systems are pivotal in numerous sectors including manufacturing, retail, and logistics. They provide a reliable and efficient means of transporting products, materials, and goods within a facility. This not only speeds up production processes but also minimizes human error and reduces labor costs. By implementing an automatic conveyor system, businesses can ensure a smoother, faster, and more cost-effective workflow.
Types of Conveyor Systems
Conveyor systems can be categorized by their functionality and the specific needs they serve. Here are a few common types:
- Belt Conveyors: Ideal for handling light to medium products, belt conveyors offer versatility and affordability. They are commonly used in food handling and packaging industries.
- Roller Conveyors: Best suited for heavy products, roller conveyors are typically used in warehouse and assembly areas.
- Modular Conveyors: As the name suggests, these conveyors are flexible and can be customized to fit various shapes and sizes, making them perfect for industries requiring versatility in their operations.
Choosing the Right Material for Your Conveyor System
Selecting the appropriate material for a conveyor system is crucial as it affects the system’s longevity, functionality, and maintenance needs. Here are some popular materials used in the construction of conveyor systems:
- Metal: Known for its durability and strength, metal is a common choice for industrial environments where heavy loads and high impact are typical.
- Plastic: Offering a lightweight and flexible option, plastic conveyors are ideal for light applications and offer corrosion resistance.
- Rubber: Rubber belts are used in environments where grip and cushioning are necessary, such as the transport of delicate items.
Optimizing Your Space with Automatic Conveyor Systems
Integrating an automatic conveyor system requires strategic planning to maximize space and enhance efficiency. Consider the layout of your facility and the nature of the items being transported. Utilizing vertical conveyors or spiral conveyors can help in making the most out of limited spaces, while telescopic conveyors are useful for loading and unloading trucks efficiently.
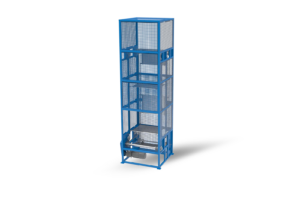
Maintenance Tips for Conveyor Systems
Regular maintenance is key to extending the lifespan and enhancing the efficiency of your automatic conveyor system. Routine checks for wear and tear, proper lubrication of moving parts, and timely replacement of faulty components will prevent breakdowns and ensure continuous productivity.
FAQs About Automatic Conveyor Systems
Q1: What is an automatic conveyor system? An automatic conveyor system is a mechanized device that transports materials from one point to another in a facility. It is designed to streamline processes and reduce manual handling.
Q2: How does an automatic conveyor system enhance operational efficiency? It minimizes the need for manual labor, reduces transit time and human error, and enhances the overall speed and reliability of the production or distribution process.
Q3: What are the main types of conveyor systems? The main types include belt conveyors, roller conveyors, and modular conveyors, each serving different operational needs based on the nature of the products transported.
Q4: What should I consider when choosing a conveyor system? Consider the type of materials being handled, the environment in which the system will operate, the load capacity, and the physical constraints of the facility.
Q5: How often should an automatic conveyor system be maintained? Maintenance frequency depends on the system type and usage but generally includes regular inspections, lubrication, and immediate replacement of worn-out or broken parts.
The implementation of an automatic conveyor system can profoundly impact the efficiency and effectiveness of an industrial operation. By choosing the right type, material, and maintenance strategy, businesses can greatly enhance their operational capabilities and ensure a high return on investment. Whether upgrading an existing setup or integrating a new conveyor system, the key to success lies in meticulous planning and execution.
Step into the future with SmartlogitecX, a WayZim Technologies venture, reshaping Warehouse Automation in the UK, Germany, Dubai UAE, and USA. Our mission is to provide you with advanced, efficient warehouse solutions that are a step ahead. SmartlogitecX combines global tech insights with local market expertise. Ready to upgrade your logistics? Our sales team is on hand to craft your ideal automation strategy.